The Chair of Protection Systems is dedicated to the interdisciplinary research of materials and protection systems under short-term dynamic loading. Cellular materials, such as hybrid metal foams and mechanical metamaterials in sandwich construction, are primarily used. The research areas include:
- Fabrication
- Mechanical and material characterization
- Experimentation, modeling and simulation
for application especially in the fields of crash absorbers in general, protection systems and electromobility.
Cellular materials such as metal foams and mechanical metamaterials (auxetic, chiral, pentamode, TPMS,…) are so-called microheterogeneous materials, where the global mechanical properties of a component or macroscopic material sample strongly depend on the mesostructure (pore or cell geometry and its size) as well as on the microstructure (web geometry, coating, etc.). Therefore, these materials exhibit strong structure-property correlation. For application-specific optimization of the materials, experimental and numerical characterization as well as optimization take place on all scales (microscale, mesoscale, macroscale).
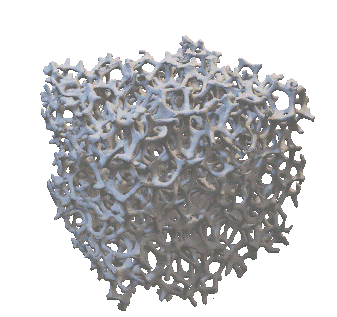
Foam
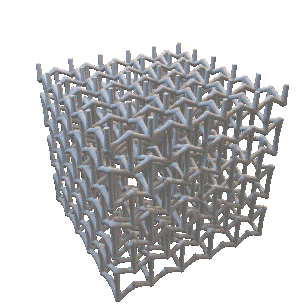
Auxetic
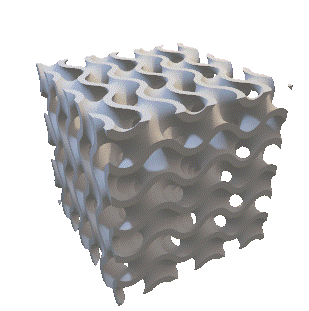
TPMS
Dynamic characterization of modified auxetic structures by
Use of a drop tower
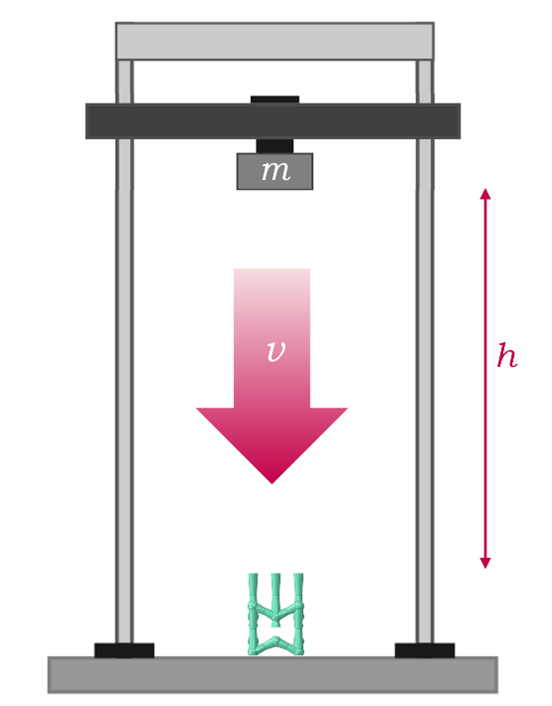
Due to the continuous increase in requirements for modern structures in many areas, the demands on the materials used are also growing. In order to meet the increasingly complex requirements, modern materials must be optimized for the corresponding application and fulfill a variety of tasks. For this purpose, nature is often used as a prime example, which does not use solid materials for load-bearing structures, but rather porous and cellular structures. Some of these structures can be summarized under the term auxetic materials. These are defined by a negative Poisson’s ratio, which leads, among other things, to a higher fracture toughness, high volume-related energy dissipation and a low density, which enables auxetic materials to be used in ballistic and explosion protection, as energy absorbers or in lightweight construction. Since most materials are often subjected to dynamic loads in reality, characterization of the rate-dependent deformation behavior is a key component in determining the materials characteristics. One method of dynamic material characterization is the usage of drop weight testing. This involves dropping a weight from a defined height onto the sample so that the potential energy of the “impactor” is converted into kinetic energy and transferred to the sample. By varying height and weight, for example, different strain rates can be realized to cover a wide range of applications.
Responsible: Alexander Engel
Optimized Material Design using Machine Learning
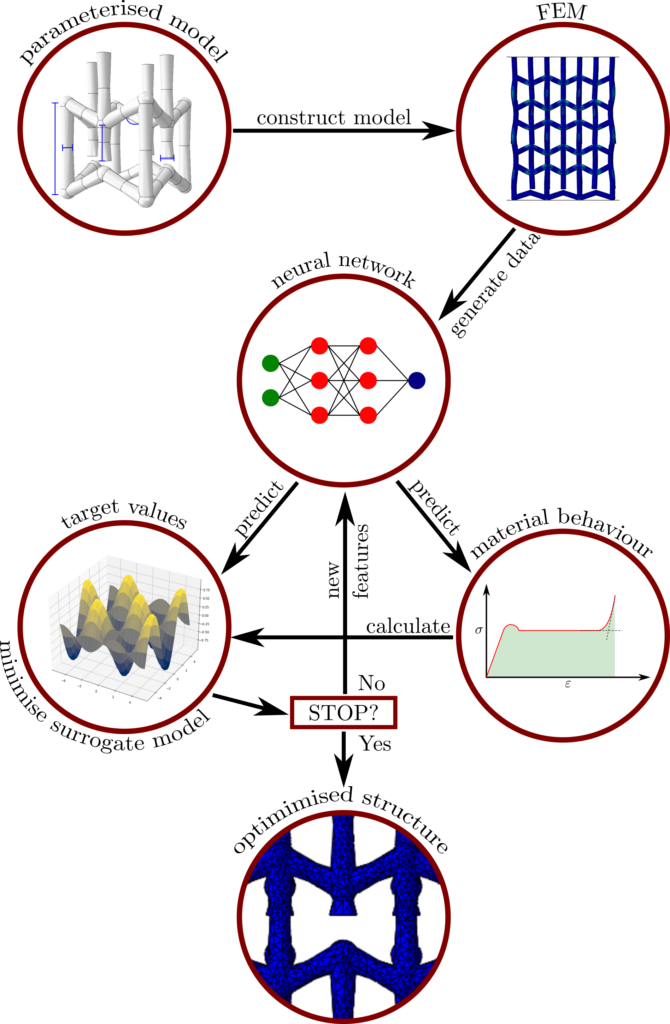
The material of the future should be stronger, lighter, multifunctional, better all around and optimized for the application. Additive manufacturing and design and optimization possibilities on the computer, such as finite element simulations, make many investigations possible today. Especially in the case of mechanical metamaterials, which are characterized by unusual mechanical properties and whose microstructure offers a high potential for adaptation, methods of structural optimization can be effectively applied. However, a limiting factor here is still the computational cost of simulations of the microstructure. In this project, machine learning, specifically neural networks, will be used to accelerate structure optimization and improve auxetic as well as pentamode structures for targeted use cases. The final designs will then be studied experimentally to validate the results of simulation and optimization.
Responsible: Stefan Bronder
Scaling and Transfer Effect in Reactive Materials
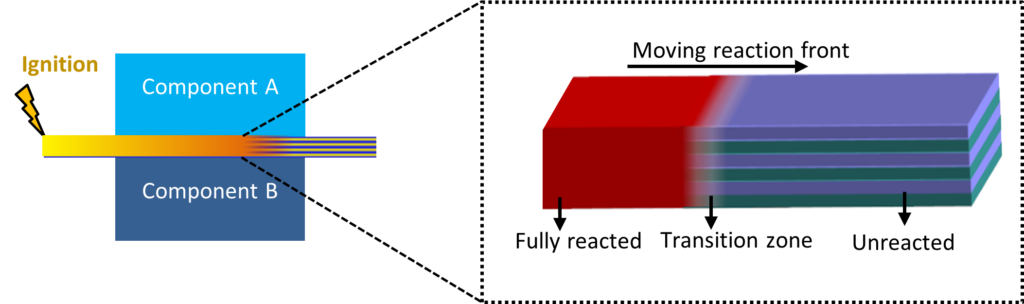
The outstanding feature of self-propagation reactions is the capability to release heat of reaction on a temporal and spatial scale that allows to sustain and propagate the reaction after a local ignition. The components of a reactive multilayer react to form an alloy and can be used to join components in a similar way to an intelligent welding process. Since the reaction is controlled by heat and material transport, the arrangement of the reactive multilayers plays a decisive role in their properties.
The aim of this project is to research basic rules and laws for controlling or slowing down the course of the reaction and phase formation through two- and three-dimensional structuring of the reactive multilayer systems made of nickel and aluminium. In this regard the effect of the lateral dimensions, the spatial arrangement and the geometric shape of the structured elements of the reactive multilayer systems on the ignition behaviour, the propagation velocity of the reaction front and the phase formation will be investigated.
Responsible: Farshad Daneshpazhoonejad
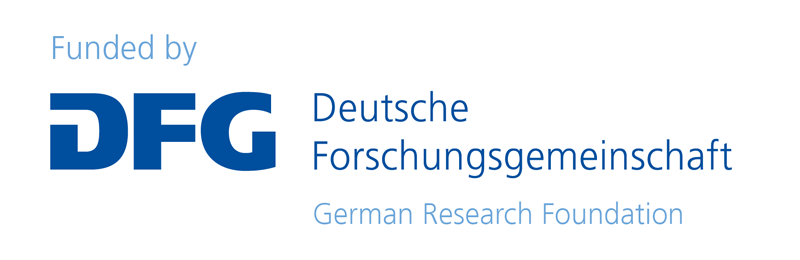
Funding code: JU 2962/9-1
Project Partner
Technical University Ilmenau
- Nanotechnology Group, Dr. rer. nat. Jörg Pezoldt
- Production technology Group, Univ.-Prof. Dr.–Ing. habil. Jean Pierre Bergmann
Simulation of an open-cell structure with improved fatigue properties for application in elastocalorics
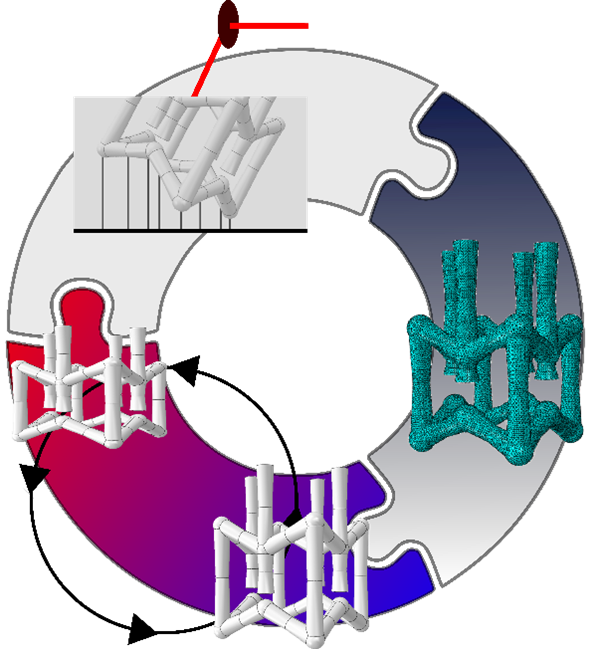
Modern cooling systems are usually based on the compression of gases. Replacing these gases with solid-state systems offers a climate-friendly alternative with no greenhouse potential. A promising material for use in an elastocaloric cooling system is Nitinol, a shape memory alloy consisting of nickel and titanium. The high potential of this material lies in the large amount of latent heat that is released or absorbed as a result of mechanical stress. This makes it possible to generate large changes in ambient temperature. Combined with the low mechanical work required for deformation, an extremely efficient and climate-friendly cooling system can be developed.
The aim of the project is to develop a structure suitable for the application described above. The process starts with an FE simulation of different possible structures.
Based on this, the 3D models found will be manufactured into real components using laser powder bed fusion (LPBF). These additively manufactured samples will be used to optimize the material model for the simulation and to evaluate the results of the structural study.
Responsible: Michael Fries
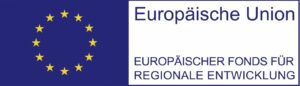
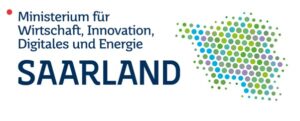
Project Partner
Smart Material Systems , Saarland University, Saarbrücken
Institute of Production Engineering, Saarland University, Saarbrücken
Optimization of the electrochemical manufacturing process of open-pore Ni/PU hybrid foam structures
The project comprises the electrochemical production and experimental characterization of cellular hybrid materials using established and further developed measurement methods, as well as the simulation-based optimization of flow reactors using CFD (computational fluid dynamics). In addition to reticulated polyurethane foams, the great progress in the field of high-resolution 3D printing even makes it possible to additively manufacture complex open-porous structures and to structurally optimize them with respect to multifunctional properties by means of the electrochemical coating process. In addition to conventional gravimetry and large-area coating microscopy, spatially resolved magnetization profiles of previously remanently magnetized hybrid foams are determined and used with a suitable correlation for semi-automatic analysis of the coating thickness distribution. The findings regarding the influences of different deposition parameters contribute significantly to the optimization of the coating homogeneity. Within the cooperation project with Saarland University, Saarbrücken, the experimentally determined structural properties coupled with the coating quality of the resulting hybrid foam serve as the basis for macroscopic modeling and simulation of the deposition process.
Responsible: Francesco Kunz
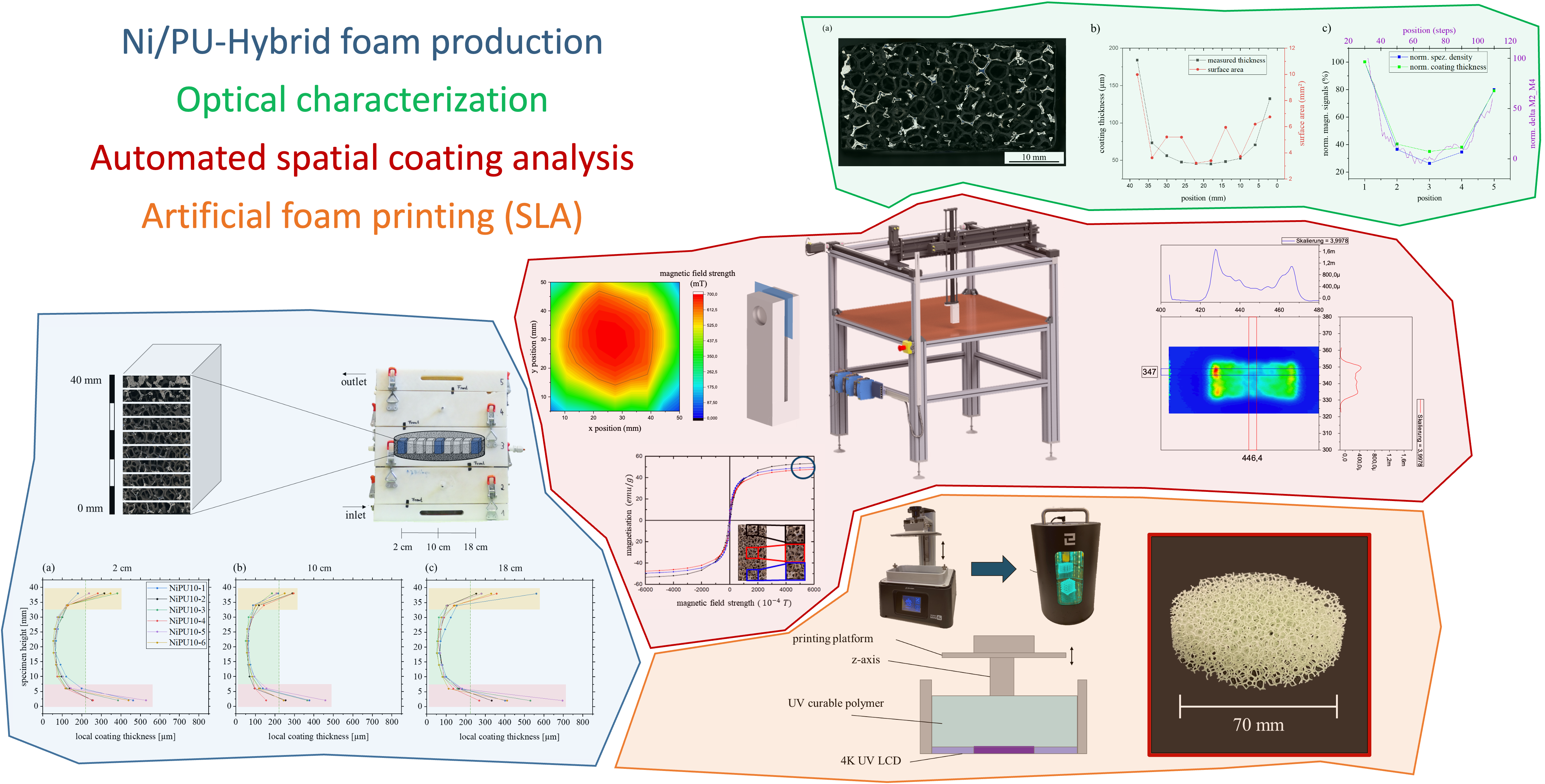
AI-Assisted Optimization of Mechanical Metamaterial Composites
Artificial intelligence pervades all areas of our modern life. Research in material sciences is no exception where Machine Learning approaches rendered themselves essential since they can circumvent various roadblocks of classical research methods.
So far, numerical simulations helped reduce experimental expenses. However, even those can become extremely time consuming when dealing with complex structures. Based on data from finite element simulations this project strives to properties of mechanical metamaterials, primarily TPMS, using a machine learning approach. The trained models are then to be used to optimize the structures regarding various properties, like specific energy absorption.
The focus here lies on the study and optimization of TPMS structure composites as well as TPMS structures with changing geometry throughout the volume.
Responsible: Sergej Grednev
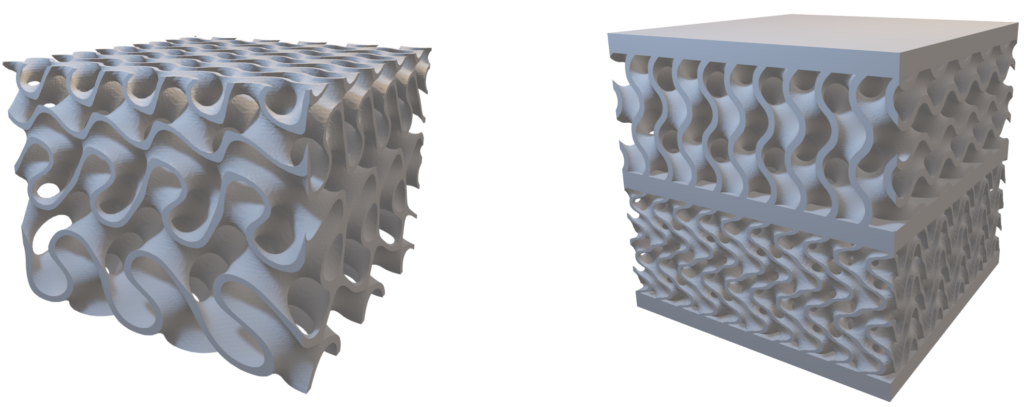
Experimental investigation of the mechanical properties of open-pore metal hybrid foams under dynamic load.
The research project comprises the production, microstructural analysis and (micro-)mechanical description of deformation mechanisms of open-cell metal foams under quasi-static, moderate and high impact velocities.
For this objective, initially different materials (Al-, Ni/PU-, Ni/Al) were applied to a stochastic open-cell structure via an electrochemical electrodeposition process and subsequently characterized regarding the specific energy absorption. The deformation mechanisms and resulting mechanical properties are further characterized at the macroscopic level on a Ni/PU model system under both moderate and high impact velocities via drop tower and SHPB experiments. The research focuses mainly on mass-dependent inertia effects and the scalability of the material system beyond the laboratory scale. Finally, the last phase of the project covers deformation mechanisms at the mesoscopic level of individual pores. The aim is to analyze micro-inertia effects as a function of pore geometry and varying preloading conditions, to conclusively correlate occurring strain rate effects on the mesoscopic level with the macroscopic component level.
Responsible: Markus Felten
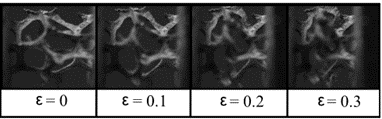
Herstellung und multiskalige Charakterisierung gradierter zellulärer Metamaterialien
Special designed materials for specific applications? Desirable thinking or soon to be reality? Cellular metamaterials can play an important role. Cellular Metamaterials are various artificial structures that exhibit, for example, special mechanical properties. Exempels are: TPMS (triply periodic minimal surface), pentamode and auxetic structures. The properties depend on the base material, the relative density, the morphology (size and shape of the pores, open or closed cell structure) and the topography (regular or irregular pore distribution). Cellular hybrid metamaterials are a special case. Here, a template (made of polymer or metal) can be coated using electrochemical deposition. Additive manufacturing can thus achieve many degrees of freedom in the structure. But electrochemical deposition can also be used to set various parameters, such as a gradient in the coating thickness or a material gradient, which can consist of a hard metal (Ni) and a soft metal (Cu), for example.
By using gradients within the structures, for example by changing the relative density, the material or the structure, special properties for specific, technical applications may can be achieved. The aim of this project is to introduce different gradients into the structures and to evaluate their mechanical properties by using simulations and experiments.
Responsible: Laura Lindner
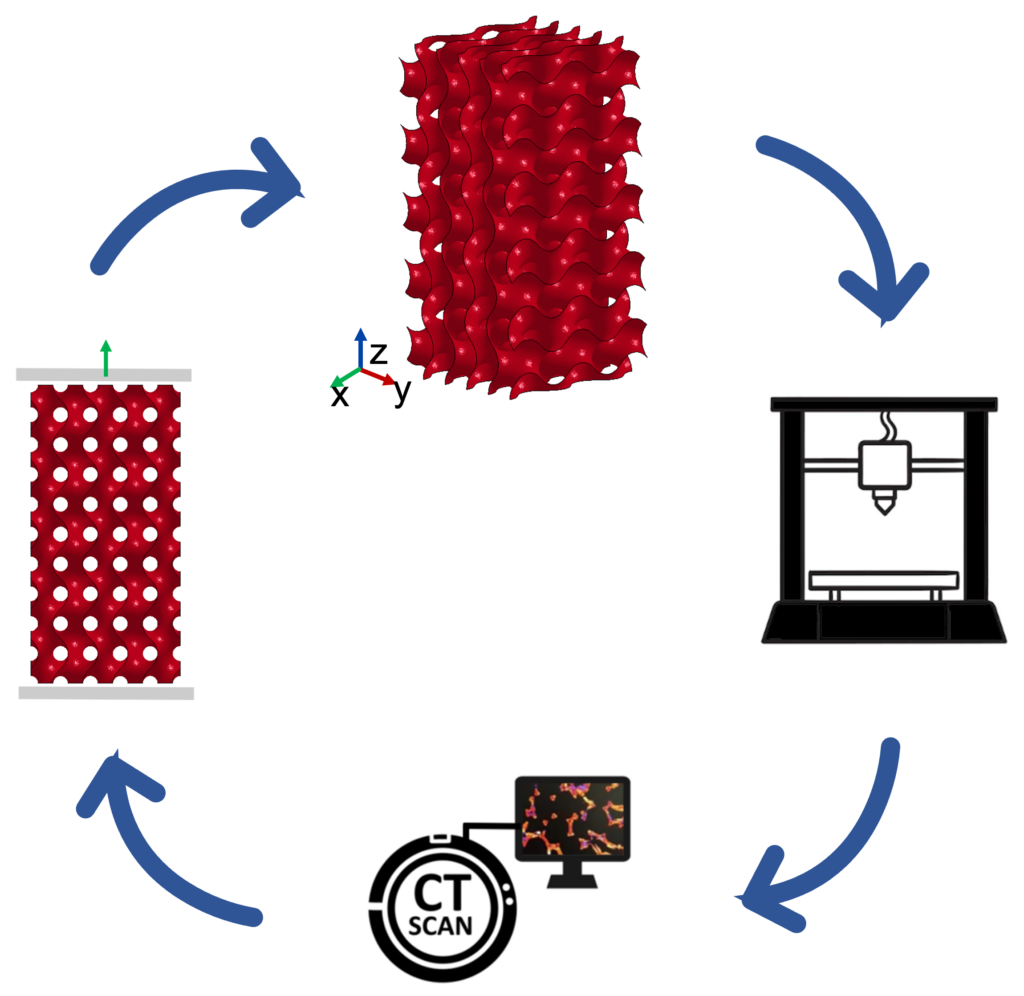
Project Partner
Czech Technical University Prague
University of Maribor
Institute of Theoretical and Applied Mechanics of the Czech Academy of Sciences
Connection of cellular hybrid materials
The progressive scarcity of resources demands efficient use of existing raw materials. To meet this demand, the primary goal is to research versatile strategies and materials and make them applicable. Metallic foams offer extremely efficient material utilization and interesting mechanical properties as a result of their enormously high porosity. The material class of metallic foams combines many demands into a lightweight material, such as low weight, high stiffness and large energy absorption.
An important step toward successful industrial application is a joining technology that can be integrated into the manufacturing process of the metal foams. In addition to the type of joining technology, the mechanical strength of the resulting joint is of great interest.
In the production of nickel/polyurethane hybrid foams, mechanical connecting elements (inserts) can be incorporated into the polymer foam substrate prior to electrochemical coating with nickel. These connecting elements are attached by deposition of the nickel. In this process, it is important for the production of a homogeneous nickel layer that all surfaces to be plated have uniform conductivity and that the surface portions not to be plated are appropriately shielded.
The mechanical characterization of the connection between insert and metal foam is carried out by realizing different loading conditions. The foam structure is clamped in a suitable clamping device and the insert is subjected to both uniaxial and multiaxial loads.
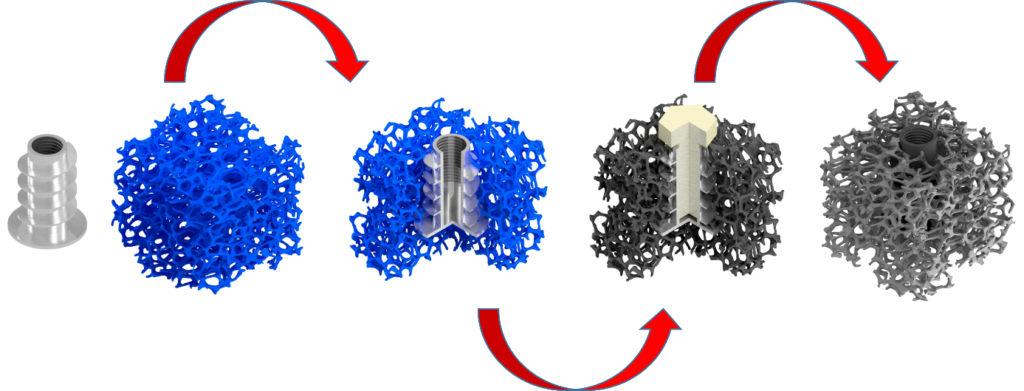
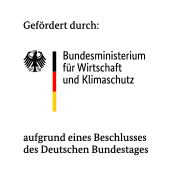
Collaborative project under the TTP Lightweight Structures Program:
“HSF – Novel joining technology for lightweight impact structures made of hybrid foams”.
Subproject: Development and mechanical characterization of the joining concepts
Funding code: 03LB1011D
Development of non-destructive in situ characterization methods for the prediction of the damage state.
The characterization of metamaterials is much more complex than for DIN specimens due to the coupling of structural and material behavior.
For this purpose, a multimodal testing method is developed to characterize the damage behavior as well as potential damage localization of complex structures. In particular, fatigue tests are performed on metamaterials at various scales with test-accompanying acoustic and electrical characterization to non-destructively predict service life and identify critical, already damaged areas in future industrial applications.
Responsible: Rebecca Kose
Project Partners
Fraunhofer IZFP MatBeyoNDT group, Saarbrücken
The project is financed by the Attract grant 025 -601314 “MatBeyoNDT” of the Fraunhofer Gesellschaft
Letzte Änderung: 26. October 2023